### How Can Mobile Mechanics Minimize Their Workers’ Comp Insurance Costs in 2025?
For mobile mechanics, workers’ compensation insurance is a necessary expense—but it doesn’t have to be a financial burden. As the industry continues to evolve in 2025, business owners can take proactive steps to reduce their workers’ comp costs while maintaining a safe and productive workforce. By focusing on prevention, proper worker classification, and strategic insurance planning, mobile mechanics can minimize risks and lower their premiums.
One of the most effective ways to control workers’ comp costs is by implementing strict safety protocols and comprehensive training programs. Preventing injuries before they happen not only protects employees but also reduces costly claims. Additionally, investing in the right tools and equipment helps minimize workplace hazards, further decreasing the likelihood of injuries.
Beyond safety measures, correctly classifying workers is crucial to avoiding unnecessary premium costs. Misclassification can lead to overpayment or even penalties. Working with an experienced insurance broker can help mobile mechanics navigate coverage options and secure the most cost-effective policy. Finally, encouraging return-to-work programs can help injured employees recover while reducing the financial impact of claims.
By focusing on these key strategies, mobile mechanics can keep their workers’ compensation costs under control while fostering a safer and more efficient work environment. In the sections ahead, we’ll explore each of these approaches in detail to help mobile repair businesses thrive in 2025.
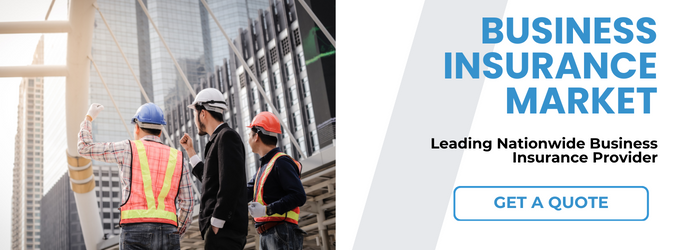
### Implementing Strict Safety Protocols and Training Programs
One of the most effective ways mobile mechanics can minimize their Workers’ Comp Insurance costs in 2025 is by implementing strict safety protocols and comprehensive training programs. Workplace injuries are a primary driver of high insurance premiums, and the more preventive measures a business takes, the lower its risk of costly claims. By enforcing clear safety guidelines, ensuring compliance with industry regulations, and fostering a culture of caution, mobile mechanics can significantly reduce workplace accidents and injuries.
A well-structured training program is essential in equipping employees with the knowledge and skills needed to perform their jobs safely. Regular safety training sessions can help mechanics understand best practices for handling hazardous materials, using tools correctly, and identifying potential risks before they lead to accidents. Additionally, ongoing education about ergonomics and injury prevention can help reduce strain-related injuries, which are common in physically demanding jobs like auto repair.
Beyond reducing the likelihood of workplace injuries, a strong safety culture can also have financial benefits. Insurance providers often consider a company’s safety record when determining premiums, meaning that businesses with fewer claims and a commitment to safety may qualify for lower rates. By investing in safety protocols and training programs, mobile mechanics not only protect their employees but also create opportunities for long-term cost savings on Workers’ Comp Insurance.
### Utilizing Proper Tools and Equipment to Reduce Injury Risks
One of the most effective ways mobile mechanics can minimize their Workers’ Comp Insurance costs in 2025 is by utilizing proper tools and equipment to reduce injury risks. The nature of mobile mechanic work involves frequent lifting, handling of heavy parts, and working in various environments, which can lead to workplace injuries if proper precautions aren’t taken. By investing in high-quality, ergonomic tools and equipment, mechanics can significantly lower the chances of strains, sprains, and other musculoskeletal injuries that often result in costly insurance claims.
For example, using hydraulic lifts, creepers, and power-assisted tools can help reduce the physical strain on mechanics, preventing common injuries like back pain and repetitive stress disorders. Additionally, ensuring that all tools and equipment are well-maintained and in proper working condition minimizes the risk of malfunctions that could lead to accidents. Employers should also provide personal protective equipment (PPE) such as gloves, safety glasses, and knee pads to further enhance safety.
Beyond just providing the right tools, mobile mechanics should be trained on how to use them correctly. Proper training on tool handling, lifting techniques, and safety best practices can go a long way in preventing workplace injuries. By prioritizing the use of appropriate tools and ensuring employees are well-trained, mobile mechanics can create a safer work environment, leading to fewer injury claims and ultimately reducing Workers’ Comp Insurance costs.
### Classifying Workers Correctly to Avoid Unnecessary Premium Costs
One effective way for mobile mechanics to minimize their Workers’ Comp Insurance costs in 2025 is by ensuring that all workers are classified correctly. Insurance premiums are heavily influenced by worker classification codes, which are determined based on job duties and associated risk levels. Misclassifying employees—whether intentionally or unintentionally—can lead to higher premiums or even penalties if an audit reveals discrepancies.
For mobile mechanics, distinguishing between independent contractors and full-time employees is crucial. Independent contractors may not require Workers’ Comp coverage, depending on state regulations, while full-time employees typically do. Proper classification not only ensures compliance with labor laws but also prevents unnecessary insurance costs. Businesses should regularly review job descriptions and consult with insurance professionals or legal advisors to maintain accurate worker classifications.
Additionally, using the correct industry codes when reporting to insurance providers is essential. Mobile mechanics who perform primarily diagnostic work may fall into a lower-risk category than those engaged in heavy repairs or roadside assistance. By accurately categorizing workers and their job duties, mobile mechanics can avoid overpaying on premiums and ensure they are only paying for the coverage they truly need.
### Partnering with an Experienced Insurance Broker for Cost-Effective Coverage
One of the most effective ways mobile mechanics can minimize their Workers’ Compensation Insurance costs in 2025 is by partnering with an experienced insurance broker. A knowledgeable broker understands the complexities of Workers’ Comp policies and can help mechanics find the most cost-effective coverage tailored to their specific business needs. By working with a broker, mobile mechanics can access better rates, identify potential premium discounts, and ensure they are only paying for the coverage they truly need.
An experienced broker can also assist in risk assessment and management strategies, helping mobile mechanics implement preventative measures that reduce workplace injuries. They can provide insights into industry trends, regulatory changes, and cost-saving opportunities that might otherwise be overlooked. Additionally, they can guide business owners through the claims process, ensuring that claims are handled efficiently to prevent unnecessary increases in insurance premiums.
By leveraging the expertise of an insurance broker, mobile mechanics can focus on running their business while maintaining compliance with Workers’ Compensation regulations. This partnership not only helps lower insurance costs but also enhances overall workplace safety, ensuring a more secure and financially sustainable operation.
### Encouraging Return-to-Work Programs to Lower Claims Impact
One effective way for mobile mechanics to minimize their Workers’ Comp Insurance costs in 2025 is by implementing return-to-work programs. These programs help injured employees transition back into the workforce as soon as they are medically able, reducing the overall impact of a claim on the business. By offering modified duties or light work assignments, employers can keep injured workers engaged and productive while they recover. This approach not only lowers the total amount paid out in claims but also helps maintain workplace morale and efficiency.
A well-structured return-to-work program demonstrates to insurance providers that the business is proactive about managing workplace injuries. Insurers often offer lower premiums to companies that actively work to reduce the duration and severity of claims. Additionally, keeping employees engaged in some form of work rather than being completely off the job can prevent long-term disability claims, which tend to be more costly.
Beyond cost savings, return-to-work programs benefit both employers and employees by fostering a supportive work culture. Injured workers are less likely to feel isolated or disconnected from their jobs, which can improve job satisfaction and retention rates. By prioritizing early intervention and gradual reintegration, mobile mechanics can create a safer, more cost-effective work environment while maintaining productivity and controlling insurance expenses.