In the fast-paced world of mobile mechanics, the risk of injury lurks in every repair job. From roadside fixes to full-service repairs, the safety of technicians is paramount not only for their well-being but also for the financial health of the business. High rates of accidents and injuries can lead to skyrocketing insurance costs, making it essential for business owners to seek proactive measures to minimize risks. This article explores five crucial steps that mobile mechanic business owners can take to enhance safety, reduce the likelihood of workplace injuries, and thereby potentially lower insurance premiums.
First, implementing comprehensive training programs ensures that all technicians are well-versed in the latest safety practices and repair techniques. Second, enforcing strict safety protocols and proper equipment use can significantly mitigate the risk of accidents. Regular maintenance and inspection of equipment is another key step, as well-maintained tools are less likely to fail and cause injury. Investing in high-quality tools and equipment can further enhance safety and efficiency, while developing an effective incident reporting and response system ensures that any accidents are dealt with swiftly and lessons are learned to prevent future incidents. By addressing these areas, mobile mechanic businesses can create a safer working environment and a more sustainable business model.
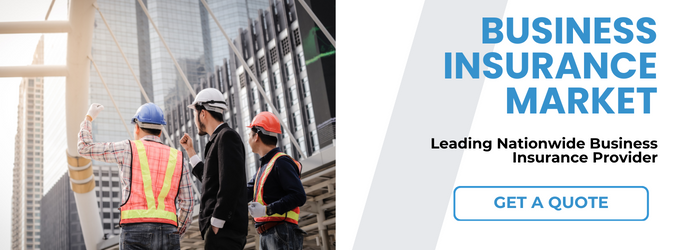
Implementing Comprehensive Training Programs
In a mobile mechanic business, one of the most effective steps to reduce the risk of injury is implementing comprehensive training programs. Such programs not only equip mechanics with the necessary skills to perform their tasks efficiently but also emphasize the importance of safety in every aspect of their work. A well-designed training program covers a range of topics including the correct handling of tools and equipment, understanding of the mechanical and electronic systems they will be working on, and the application of safety measures specific to mobile operations.
Training should also include first aid and emergency response skills to prepare mechanics for handling accidents should they occur. This not only helps in reducing the severity of injuries but also instills a culture of safety among the team members. Regular refresher courses are crucial to keep the mechanics updated on the latest safety protocols and technological advancements in automotive repair.
Moreover, comprehensive training extends beyond technical skills. It should also cover ergonomic practices to prevent overexertion and repetitive strain injuries, which are common in mechanic jobs. Educating workers about the risks of ignoring safety procedures can lead to a more conscientious approach to tasks, significantly reducing the likelihood of accidents.
Implementing such training programs can be seen as an upfront investment but pays off by minimizing costly accidents, reducing downtime, and potentially lowering insurance premiums as the business demonstrates a commitment to safety. Insurance companies often provide better rates to businesses that actively work to minimize risk, viewing them as lower-risk clients. Hence, a robust training program is not just about compliance or reducing injuries, but it’s also a strategic approach to managing operational costs in a mobile mechanic business.
Enforcing Safety Protocols and Equipment Use
Enforcing safety protocols and proper equipment use is crucial in reducing the risk of injuries in a mobile mechanic business. This step involves creating and implementing a set of rules and guidelines that every employee must follow to ensure their safety as well as the safety of their colleagues and clients. These protocols typically cover everything from the correct way to lift heavy items to the proper use of personal protective equipment (PPE).
For instance, mechanics should always wear gloves, goggles, and ear protection when necessary to protect against burns, cuts, and hearing loss. Ensuring that all employees are equipped with the right tools and safety gear not only minimizes the risk of accidents but also demonstrates to insurance providers that your business takes risk management seriously, potentially leading to lower insurance premiums.
Moreover, regular safety meetings and training sessions can help reinforce these protocols and keep safety at the forefront of your employees’ minds. It’s important that these training sessions are held consistently and updated regularly to accommodate new safety practices or changes in equipment. By maintaining a strict adherence to safety standards, you can create a safer working environment that reduces the likelihood of injuries and insurance claims.
Regular Maintenance and Inspection of Equipment
Regular maintenance and inspection of equipment are crucial steps for reducing the risk of injury in a mobile mechanic business. This practice not only ensures that all tools and machinery are functioning correctly but also helps in identifying potential hazards before they lead to accidents. Regular checks can extend the lifespan of equipment, which in turn, contributes to safer working conditions and can significantly lower insurance costs by minimizing the risk of costly claims resulting from equipment failures.
When implementing a maintenance schedule, it is important to follow the manufacturer’s guidelines for each piece of equipment. This includes routine checks, servicing, and immediate repair of any wear and tear. Keeping a detailed record of maintenance and inspections can also be beneficial, both for ensuring compliance with safety regulations and for use in insurance assessments. These records provide proof that the business is taking proactive steps to maintain a safe environment, which could be influential in negotiating lower insurance premiums.
Additionally, training employees on the proper handling and upkeep of equipment is essential. This not only empowers them to perform their tasks more efficiently but also reduces the likelihood of improper use, which is a common cause of workplace injuries. By fostering a culture of safety and responsibility, a mobile mechanic business can improve its operational reliability and safety record, leading to reduced insurance costs and enhanced overall performance.
Investing in Quality Tools and Equipment
Investing in quality tools and equipment is a crucial step for reducing the risk of injuries in a mobile mechanic business, which can also help in lowering insurance costs. High-quality tools and equipment are generally more reliable and safer to use. They are designed with better safety features, which minimize the risk of accidents that can lead to injuries. For instance, tools with non-slip grips and ergonomic designs reduce the strain on the body and decrease the likelihood of repetitive strain injuries.
Furthermore, quality tools are often more durable and less likely to break or malfunction during use. This reliability can prevent situations where improvised or substandard equipment leads to accidents. Additionally, using high-quality equipment can enhance the efficiency and effectiveness of the repair work, leading to faster job completion and reduced exposure to potentially hazardous situations.
Insurance companies often recognize the investment in quality tools and equipment as a commitment to safety and risk management. As a result, businesses that make these investments may benefit from lower insurance premiums. Insurers see these companies as lower risks because they are less likely to make claims related to equipment failures or related injuries.
Moreover, maintaining a reputation for using high-quality equipment can also attract more clients who are looking for professional and reliable service. This can lead to increased business opportunities, which helps offset the initial cost of investing in better tools and equipment. Thus, while the upfront cost might be higher, the long-term benefits in terms of safety, efficiency, client satisfaction, and insurance cost savings make this investment worthwhile.
Developing an Effective Incident Reporting and Response System
Developing an effective incident reporting and response system is a critical step for reducing the risk of injury in a mobile mechanic business. This system serves as a foundational component of a broader safety program, helping to ensure that all incidents are reported promptly and accurately, and that appropriate responses are implemented swiftly to mitigate any immediate risks or dangers.
An effective incident reporting system begins with clear guidelines on what constitutes an incident, ensuring that all employees understand which events need to be reported. This includes not only accidents that result in injury but also near misses, which can provide valuable insights into potential hazards before they result in harm. By encouraging the reporting of near misses, businesses can proactively address safety issues and prevent future injuries.
The response part of the system is equally important. Once an incident is reported, a structured process should follow to investigate and analyze the cause of the incident. This process should involve not only rectifying the immediate issue but also identifying underlying causes that need to be addressed to prevent recurrence. This might involve revising work procedures, enhancing training programs, or upgrading equipment.
Finally, maintaining records of all incidents and the responses to them is crucial. These records help businesses to track trends over time, identify areas for improvement, and provide evidence of compliance with safety regulations. Moreover, a well-documented incident reporting and response system can demonstrate to insurance companies that the business is serious about managing risks, which may lead to lower insurance costs.
Implementing such a system not only helps in reducing the likelihood of workplace injuries but also fosters a culture of safety and responsibility among employees. It shows a commitment to the well-being of employees, which can enhance morale and productivity while reducing turnover and associated costs.